Новые отрасли промышленности, бурно развившиеся во второй половине ХХ века (аэрокосмическая, атомная, электроэнергетическая) предъявили новые требования ко многим сортам стали. Космической и атомной отраслям необходимы материалы, способные работать в вакууме, при температуре от нескольких тысяч градусов до почти абсолютного нуля, в условиях высокой радиации и вибрации, в химически-агрессивных средах... Стали, способные выдерживать такие условия и нагрузки относятся к категории специальных.
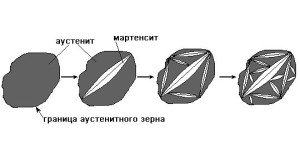
Они могут отличаться от обычных сортов стали
- особым химическим составом
- специальным способом изготовления и выплавки
- специальным способом обработки
Обычно спецстали отличаются от остальных по всем трем параметрам (хотя в принципе достаточно наличия и одного из данных факторов, чтобы определить сталь как специальную). В настоящее время доля специальных сталей в сортаменте металлургической промышленности постоянно растет, что и не удивительно: спрос на такую сталь существует машино- и судостроении, на транспорте... не говоря уж о военно-промышленном комплексе.
К специальным сталям относятся сплавы с повышенным содержанием никеля, хрома, вольфрама, молибдена, ванадия и др. элементов.
Главным признаком легированной специальной стали является то, что легирующие добавки вводятся в ее состав специально для достижения определенных свойств металла.
В маркировке таких сталей легирующие добавки обозначаются буквами:
- Х - хром (Cr)
- Н – никель (Ni)
- К – кобальт (Co)
- М – молибден(Mo),
- В – вольфрам(W),
- Т – титан (Ti)
- Д – медь (Cu)
- Г – марганец (Mn)
- С – кремний (Si)
- Ф – ванадий (V),
- Р – бор (B)
- А – азот (N),
- Б – ниобий(Nb)
- Е – селен (Se)
- Ц – цирконий(Zr),
- Ю – алюминий(Al)
- Ч – редкоземельные элементы.
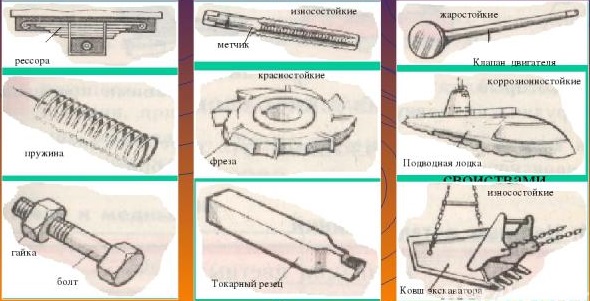
Например, для придания стали повышенной жаростойкости, в ее состав добавляют хром (а также отчасти алюминий и кремний).
Вступая в реакцию с кислородом, эти элементы образуют в структуре металла особо плотные и прочные структуры из тугоплавких кристаллов, что позволяет металлу выносить высокие температуры.
Увеличивают жаростойкость стальных сплавов и добавки таких металлов, как титан, ниобий или тантал.
Такие стальные сплавы называют еще сильхромами, к ним, например, относятся:
- 08Х17Т
- 15Х25Т
- 15Х6СЮ
- 36Х18Н25С2
Первые две цифры в их маркировке обозначают сотые доли процента углерода, процент легирующих добавок определяют цифры после маркирующей буквы (кроме тех случаев, когда содержание добавки составляет мене одного процента).
Следовательно, в жаропрочной стали 36Х18Н25С2 будет 0,36% углерода, 18% хрома, 25% никеля и 2% кремния. А в марке 15Х6СЮ при 0,15% углерода и 6% хрома будет еще около одного процента кремния и алюминия.
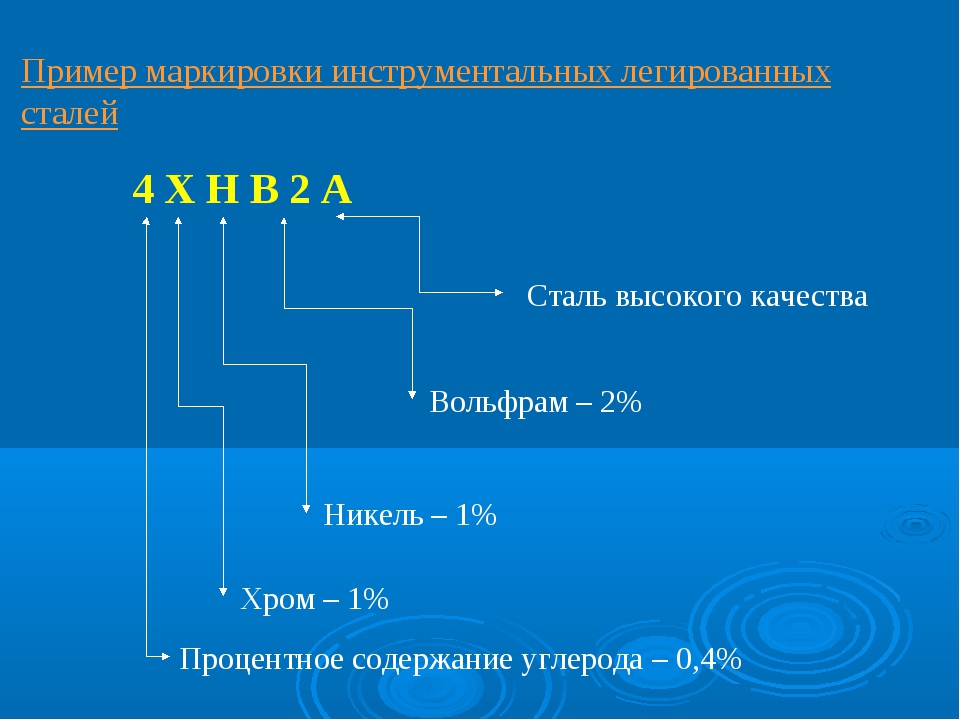
Хром и никель, будучи добавленными в состав стали придают ей также и устойчивость к коррозии. При этом по своей структуре хромо-никелевые нержавеющие стали делятся на несколько видов, среди коих наибольшее значение получили:
- ферритная (F)
- мартенситная (C)
- аустенитная (A)
Ферритная хромистая нержавейка содержит очень мало углерода, имеет малую твердость и может притягиваться магнитом. В отечественной маркировке такая нержавеющая сталь определяется чаще всего по сочетанию 12Х17. Ферритные стали отличаются высокой жаропрочностью и плохой свариваемостью. В этой связи из нее производят преимущественно цельнокатаные изделия: листовой прокат, трубы и прутки.
Мартенситные сплавы наиболее тверды, но менее устойчивы к коррозии, и тоже могут (но не всегда) проявлять магнитные свойства. Их использование уместно при изготовлении столовой посуды, производстве металлорежущего инструмента и в некоторых областях машиностроения.
Аустенинтная нержавейка отличается высоким содержание хрома (до 20 %) и никеля (до 15 %), хорошими антикоррозийными свойствами и отсутствием магнитных свойств. Она наиболее популярна у потребителей, поскольку достаточно легко поддается обработке. Аустенитные сплавы широко употребляются в промышленности и особо популярны при использовании в крепежных элементах.
Кислотоустойчивость стали увеличивается также при введения в ее состав никеля и молибдена. Придают устойчивость к кислотам и добавки марганца и меди.
Например, в стали 10Х17Н13М2Т кроме 0,1% углерода, 17% хрома и 13% никеля будет еще 2% молибдена и около процента титана. Но заводская марка стали отражает ее состав не полностью. В стали марки 12Х18Н10Т кроме 0,12% углерода, 18% хрома, 10% никеля и процента титана будет еще присутствовать 0,3% меди, 0,2% марганца и 0,8% кремния. Но об их наличии можно узнать уже только в специальной справочной литературе.
Там же можно выяснить, что сталь 12Х18Н10Т относится к аустенитным и входит в группу высоколегированных термо- и коррозионноустойчивых сталей. Для получения полной информации о свойствах "нержавеек" можно еще обратиться к ГОСТ 5632–72, в котором описаны все виды специальных сталей, их химсостав, физические свойства и даны рекомендациями по применению.
Из ГОСТ 5632–72 легко понять, что к аустенитной группа сталей относится множество стальных сплаво, в том числе и так называемые нержавейки 300 серии. Они все жаропрочны, устойчивы к коррозии и поэтому очень востребованы на рынке.
Разумеется, свойства сплавов могут изменяться в зависимости от соотношения легирующих элементов. Так, примесь серы может сделать сталь более прочной, но снизит ее устойчивость к коррозии.
Например, чрезвычайно жаростойкая аустенитная сталь А1, способная работать при температуре до 1100 C, содержит довольно много серы - поэтому подвержена коррозии и не должна использоваться в кислотной среде. Но зато детали из нее незаменимы при производстве щелочей, из стали А1 делаются крекинговые узлы, установки каталитического реформинга и проч.
Надо заметить, что в процессе производства также и нелегированной стали в ее состав могут попадать различные примеси и легирующие элементы, которые присутствуют в железной руде. Такие естественные добавки обычно не оказывают заметного влияния на качество стали, но иногда их сочетание может «само собой» придавать ей особые свойства. Такое наблюдалось, например, в средневековье, когда «дамасская сталь», выгодно отличалась от всех прочих по своим качествам, просто в силу особого состава железной руды, не будучи легированной в строгом смысле этого слова. «Дамасская сталь» отличалась, как известно, сочетанием высокой прочности и гибкости (упругости).
Эти свойства современная металлургия может воспроизводить вполне целенаправленно. Например, ее близким аналогом «дамасской стали» можно считать ножевую сталь 95Х18.
Это высоколегированная хромистая нержавейка не уступает «дамасской» по твердости и устойчивости режущей кромки, и превосходит по устойчивости к коррозии. Не удивительно, что ее и по сей день используют для производства холодного оружия. Хотя основное, промышленное, предназначение данного вида стали — быть материалом для производства износостойких деталей, которые работают при температуре до 500 градусов в умеренно-агрессивных средах.
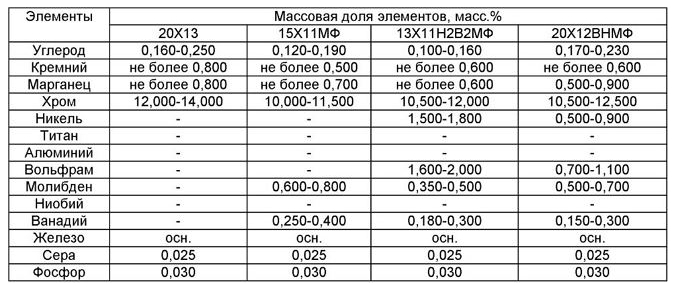
Что же касается упругости, то по этому показателю дамасскую сталь превосходит сплав 60С2А, содержащий кремний (1,6-2,0%), марганец ( 0,60-0,90%), хром (до 0,3%), никель (до 0,25%), медь ( 0,20%), фосфор и серу (до 0,025%), который используется при производстве рессор и тяжело нагруженных пружин.
Кроме того, надо отметить, что порой и очень малая доля легирующего элемента (в количестве 0,1% и менее), влияет на ее свойства весьма существенно. Поэтому "специальным составом" следует признать и беспримесно-чистое железо. Благо, что одним из примеров спецстали может служить т.н. «цементированная» сталь, в которая получается путем внедрения углерода в особо чистое железо.
Тот же процесс является и примером того, что сталь может становиться специальной и в зависимости от специального особого способа выплавки.
Свойства обычных и специальных сортов стали, имеющих один и тот же химический состав, могут сильно различаться в зависимости от того, каким технологическим путем они получены - томасовским или бессемеровским способами, в мартеновских, тигельных или электрических печах.
Примером тому могут служить стальные сплавы с содержанием 0,6-0,8% углерода и около 0,6-1% марганца.
Сплавы для продукции широкого применения (например для закаливаемых рельсов), производятся томасовским способом или в обычных мартеновских печах. Специальную сталь почти того же состава, необходимую для производства штампов и особо прочных режущих инструментов получают в электропечах; металл, подходящий для пил и лемехов выплавляют в бессемеровских и «кислых» мартеновских печах.
Разница в итоговых физических свойствах стали связана с тем, что при использовании определенных технологий плавки даже минимальные примеси различных элементов (азота, кислорода, серы и фосфора и пр.) могут оказать своё влияние на конечные свойства сплава. Из чего следует, что повлиять на свойства стали, сделав ее специальной, может и технология последующей обработки. Примером тому могут служить сорта листовой стали для глубокой вытяжки, полученные из мягкой низкоуглеродистой стали.
Сейчас активно разрабатываются технологи, которые позволяют придавать многим сортам стали специальные свойства в процессе обработки. Особенно это относится к спецэлектрометаллургии, основные направления развития которой заключаются в:
- Совершенствовании способов выплавки и переплавки агрегатов специальных составов для получения спецсталей заданного качества металла
- Разработке способов изготовления спецсталей «земного» (то есть не авиакосмического) назначения.
При этом наибольшее внимание направлено на достижение снижения себестоимости производства специальных сталей. Наиболее перспективным направлением в этой сфере считается производство специальных сплавов методами порошковой металлургии.
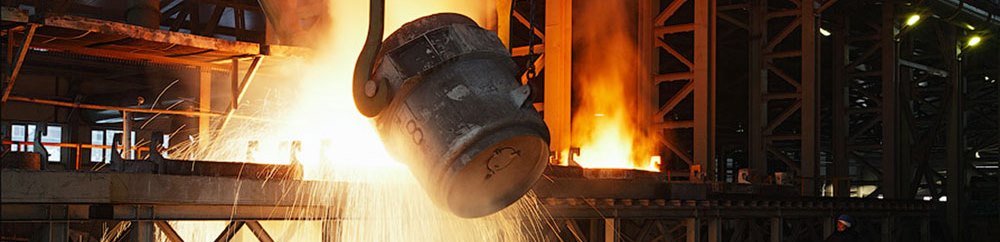